Generative Manufacturing: Transmuting Code into Physical Goods
The future of consumer goods is generative.
Today, onchain generative algorithms are primarily used in the visual arts domain, as artists write code to create digital and interactive pieces, animations, and prints. However, art is likely just the first applicable medium for this new onchain creative process. We believe onchain generative media will proliferate across every other consumer and luxury goods vertical, and this artistic process will uniquely enable a new class of physical productions through generative manufacturing.
The allure of generative collections is evident: consumers yearn for distinctive products that reflect their unique identities while also tethering them to a larger community. Through the 1/1/x model, generative algorithms accomplish this by creating singular pieces in a wider collection with cohesive aesthetics. These unique creations cater to individuals' specific tastes, allowing for granular expression within a tribe, and its success in this endeavor is showcased by the burgeoning popularity of PFP markets and the niche communities sprouting around specific generative traits.
Interestingly, generative algorithms and 1/1/x rarity distributions address the tension between mass production and customization as well. In traditional manufacturing, creating customized products on a large scale is often impractical and costly. Generative algorithms however can be directly integrated into fabrication hardware like 3d printers, CNC machines, laser printers, automatic looms, and other devices, providing feasibility in terms of production and distribution while offering scarcity and uniqueness.
This interplay between social dynamics and rarity, and digital creation and physical production, sets the stage for a new class of consumer and luxury goods that combine algorithmic randomness, end-user parameterization, and verifiable uniqueness to meet the desires of consumers.
History of Generative Manufacturing
Artists have consistently turned to technology as a means to explore new dimensions in creativity. Over time this relationship has evolved markedly, moving from pure artistic endeavors to the confluence of art and manufacturing.
-
1960s - Early Generative Art: Artists began experimenting with algorithmic processes to create artworks. Using early computers and programming languages, along with tools such as the pen plotter, artists like Manfred Mohr, Vera Molnár, and Harold Cohen began creating algorithm-driven artworks.
-
1980s - Personal Computers Software Revolution: The emergence of personal computers made digital tools more accessible. This enabled a wider range of artists to experiment with these novel artistic processes.
-
1990s to 2000s - Birth Expansion of Additive Manufacturing: As 3D printing emerged and evolved, artists saw new opportunities. Generative artists began to experiment with these tools, creating sculptures and installations directly from their software-driven designs.
-
2000s to 2010s - Digital Art Meets Digital Fabrication: As both fields matured, digital artists would collaborate with makers, architects, and designers to realize large-scale installations. Projects like the Hy-Fi tower by The Living, which used organic bricks cultivated from corn stalks and mushrooms, incorporated generative design principles in its conception and used modern manufacturing methods for its creation. It was around this time that software tools tailored to artists, like Processing, empowered them to create complex programmatic art without needing deep programming knowledge as well.
-
2010s - Maturation of Tools Methods: Generative art platforms and frameworks such as openFrameworks and TouchDesigner grew in popularity. These tools, combined with more accessible and sophisticated 3D printing, laser cutting, and CNC milling technologies, enabled seamless production. For instance, artists like Nervous System used generative algorithms to design unique jewelry and apparel items that were subsequently 3D printed.
-
2020s - Convergence Collaboration: The line between art, design, and manufacturing has become increasingly blurred. Art installations, architectural structures, and even everyday objects now showcase the unique aesthetics and capabilities that the combination can produce. Notably, onchain art renewed interest in the field of generative art at this time, using cryptographic inputs as random seeds for onchain collections. Coupled with new primitives in the digiphysical space, we are reaching a new beachhead in the marriage of digital creation and physical production.
Today's generative artists aren’t just producing art; they’re redefining consumer goods, merging aesthetic value with functional design, and pushing the frontiers of what's possible in both art and industry.
Web3 Experiments
Within web3, there are a variety of early experiments with generative manufacturing.
Trame x CPG’s Craft Nouveau is a series of collections focused on combining traditional crafts with generative art, showcasing the ability of generative code to preserve the art styles of cultures across the globe. Navette by Alexis André was the debut collection of Craft Nouveau, wherein Alexis wrote an algorithm that generates images that are designed to be woven automatically by the Neolice Loom - an automatic loom that can ingest code to weave physical pieces.
The fx(hash) ecosystem has seen a lot of experimentation on the manufacturing side - likely due to its permissionless approach to self-publishing. Klangteppich , an evolving dynamic NFT provides instructions for a loom and allows the collector to receive a physical piece of any generated frame. Mini Dahlias hold within the metadata of the NFT the instructions to create a 3.5" x 2.0" pocket sculpture from 14 layers of laser cut alpha-cellulose mat board. Nuages possible creates variations on Joanie Lemercier’s cloud series with the outputs from the code recreated by a plotter machine in physical space.
Outside of craft and art, fashion is one of the most explored avenues for generative manufacturing. 9dcc ’s production of Iteration-002 is an early example of combining generative designs and physical products. The Iteration-002 shirts were produced live using a printer that was plugged into SnowFro’s Squiggles algorithm. The printer relied on the algorithmic randomness of the source code to determine the traits of the design printed on the shirt, and it followed the same trait distribution as the original 10k collection.
Tribute Brand also recently remixed the Chromie Squiggle algorithm to create manufactured clothing. Chromie Squiggle holders could generate personalized sweaters using their unique Chromie Squiggle, while others can generate one-of-a-kind sweaters through the original Chromie Squiggle algorithm. The drop included both a digital and physical ODDS sweater derived from the source code of Chromie Squiggle. The digital objects serve as blueprints for future sweater editions and can be used as skins in immersive environments, and each unique ODDS digital object can be redeemed for a corresponding ODDS physical sweater, handmade by Waste Yarn Project.
Other notable generative fashion projects include mmERCH and RSTLSS , both of which plan to experiment around algorithmic randomness and designs.
Taking a slightly different approach to generative goods, Deep Objects used a community curation engine to whittle down one million designs generated by their GAN AI model to a single piece. This final piece is now set to be 3d printed in a showcase of community-powered generative product creation.
The Generative Manufacturing Stack
The generative manufacturing stack can be broken down into 5 layers:
-
Creation: The initial stage where a design or concept is generated using algorithmic or AI processes.
-
Curation: The process of selecting and refining the generated designs to achieve desired outcomes or specifications.
-
Translation: The conversion of the digital design into machine-readable instructions or code to be used by the manufacturing equipment.
-
Fabrication: The physical production or manufacturing process of the design using various materials and equipment.
-
Authentication / Linking: The verification of the authenticity of the manufactured product and linking it to its digital twin to ensure provenance.
Creation Layer
The creation of a generative good starts with code. Libraries like p5.js and Processing provide powerful tools for artists and designers to create generative art. These libraries are extended through onchain randomness using seeds generated from tx hashes, token data, block headers, and more. Onchain art engines like ArtBlocks Engine and fx(hash) allow artists to easily plug these random seeds into their code and mint an artwork directly onchain.
For AI artists, this layer is focused on model development and fine-tuning to create a desired aesthetic. They typically start by selecting a pre-existing AI model, such as a generative adversarial network (GAN) as a foundation. Through backpropagation, the model weights are gradually improved to generate art that aligns with the desired style. The artist provides feedback by curating the most appealing outputs and incorporating them back into the training dataset. This iterative process continues, refining the model's performance and allowing the artist to explore different possibilities. Outside of custom models or Stable Diffusion LoRAs, there are also tools to simplify this process, such as Scenario.gg .
Curation Layer
Following the creation layer, the outputs of the code can be further refined to match a user’s preference. In the creative coding context, this is typically in the form of multiplayer parameterization like what is available with fx(hash)’s fx(params).
In the context of AI generative models, curation has typically been done via a broader community of tokenholders as is the case with Botto ’s generative algorithm and the Deep Objects’ community design process.
Studios or self-publishing is the final leg of the curation process. This is where generative studios like Trame and ArtBlocks come in to present pieces to the public, or fx(hash) as a self-publisher.
Translation Layer
Once the algorithm and design is set, the generative good must be translated into machine-readable instructions for fabrication hardware. Translation is a relatively straightforward process with the goal to recreate a piece in physical space as accurately to the original as possible.
Translation can be done in a few different ways including:
-
Artist / Collector Interpretation. The simplest way to translate an object is to leave the physical design specs up to the artist or collector. They would make decisions about how a piece should be made, the material to be used, the specific dimensions, etc.
-
Embedded Traits. A much more scalable and interesting approach is to embed the physical information needed for fabrication into the NFT itself. Traits within the metadata of the NFT define the areas of interpretation (e.g. the thread count, thread size, weave instructions, and more for a tapestry piece).
-
Direct Instantiation. A third approach is the generation of the interpretable asset directly: the generative algorithm is already adapted for the fabrication hardware, or the output of the algorithm is a 3d-printable file or the vertices of a 3d mesh.
Fabrication Layer
After translation, the generated goods are fabricated. The fabrication phase is a critical step that involves converting the virtual design into a physical object. Several techniques, such as 3d printing, CNC milling, laser cutting, robo-printers, and automatic weaving, are used to create objects with different materials and shapes.
For Trame’s first drop with Alexis Andre mentioned above, the Neolice Loom was used as the fabrication hardware. The Neolice Loom takes in the artist’s custom script and reinterprets the code into 3d space through weaving. Trame is extending into new mediums as well - the above picture highlights an experiment with generative pottery.
While specific to generative art production today, Artmatr highlights what advanced fabrication tooling can do for physical production of digital items. Artists work with the Artmatr team to submit various digital file formats such as code, 3D models, PSD files (Photoshop), vectors, and animations. Next, they define the physical ‘threads’, including parameters such as the medium (oil, UV, acrylic), substrate, dimensions, and more. Lastly, this is materialized through the use of machines like robotic arms and 6-axis printers. Different techniques such as inkjet printing, airbrushing, and extrusion are utilized, and the resulting topologies can be 2D, 2.5D, or 3D.
Authentication / Linking Layer
After the physical object is created, it needs to be linked back to its digital twin. This would be similar to digiphysical processes in other spaces like fashion. Use of near-field communication chips like those manufactured by Kong and IYK , stenography, and QR codes are just some of the techniques for linking the digital to physical and providing certification around provenance.
Check out our recent post on digiphysical infrastructure here, or our piece on digital fashion which dives into digiphysical strategies specific to fashion.
Future Possibilities
Going forward, we anticipate existing onchain generative art will act as programs for derivatives. We’ve seen this through the use of Squiggles in a variety of fashion projects, and another early example of this is Terraflows , a flow field study built on top of the Terraforms art program. This kind of networked art can lead to fascinating reinterpretations of generative art in physical space. For example, one could use the Fidenza art script to create architectural layouts for 3d printed homes.
Another interesting future possibility is the tokenization of decentralized manufacturing facilities for producing generative goods at scale in a kind of physical infrastructure network. Hobbyists and commercial manufacturers with the appropriate equipment can print or create pieces by bidding for jobs posted by collectors or artists. A token can meter this hardware network and assist with bootstrapping the initial costs of manufacturing facilities. This pairs especially well with a CC0 paradigm coupled with onchain code.
Looking even further out, synthetic biology and/or chemistry manufacturing could be an interesting avenue as well for generative qualities: for example, generative code could be used to algorithmically determine the traits of lab-grown crystals, phenotypes of plants, and more.
—
We firmly believe in a digiphysical future where online networks port into physical spaces. Generative design, which includes algorithmic randomness, end-user parameterization, and verifiable uniqueness, is one such program we expect to port over - and existing fabrication hardware is capable of bringing this to fruition.
If you are building at the intersection of art and technology + digital and physical, please reach out to us .
Disclaimer: The content of this article solely reflects the author's opinion and does not represent the platform in any capacity. This article is not intended to serve as a reference for making investment decisions.
You may also like
RFCUSDT now launched for futures trading and trading bots
Bitget Spot Bot adds RFC/USDT
Checkmate: How Adopting a BRICS Payment System Might Erode the Dollar’s Dominance in Trade Markets
Fake McAfee pop-ups fuel Bitcoin and gold scams
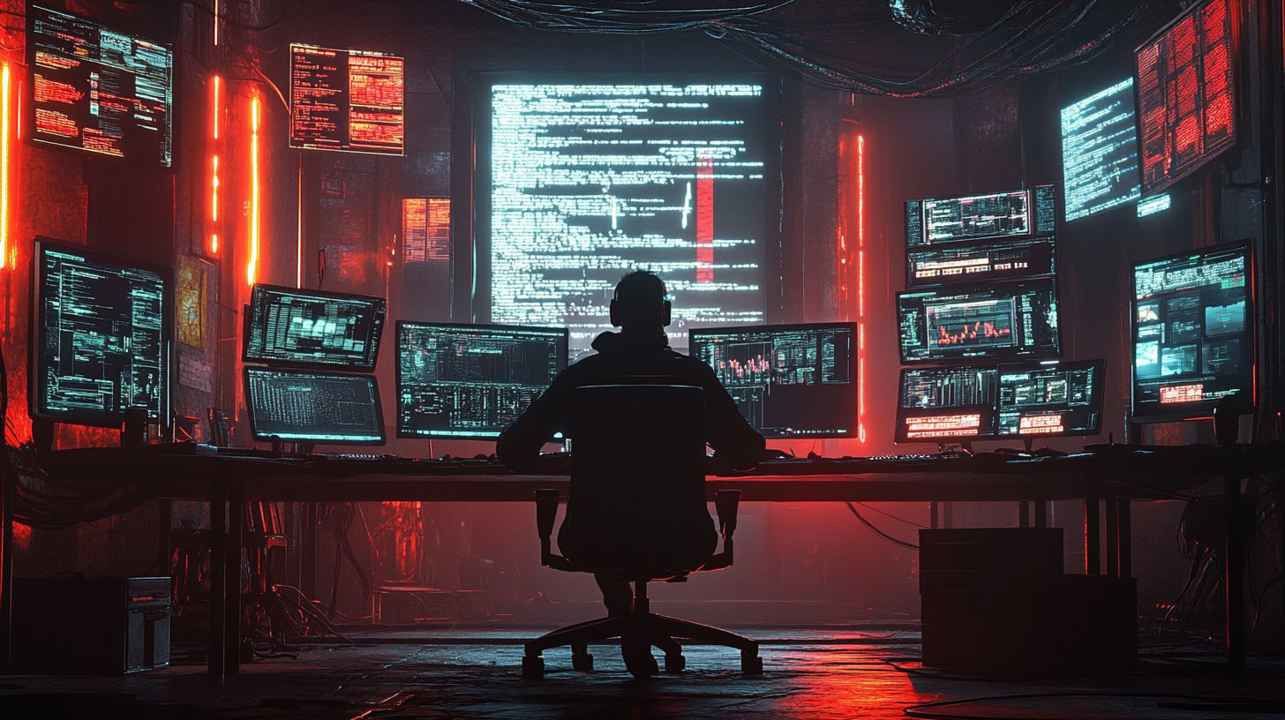
Trending news
MoreCrypto prices
More








